Pool Production Process
Step 1:
Mould Ready For Production
Each constructed pool is assigned a unique 5-digit number for tracking purposes after it departs from the site and for quality control procedures. The number is imprinted on a waxed label, which is removed from the mold upon the pool’s release, leaving a distinct indentation of the digits.
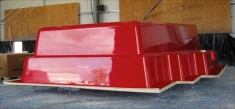

Step 2:
Gelcoating
The 8.5m Venice is beautifully finished with a gel-coat in a striking Royal Ocean colour, expertly applied at a thickness ranging from 0.8mm to 1.0mm. Similarly, the 7.2m Venice showcases a gel-coat in a warm Beach hue, applied with the same precision at a thickness of 0.8mm to 1.0mm.

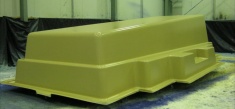
Step 3:
Tie-Laying With Vinyl Ester
VE is applied on at 1.5mm to 2.0 mm thick.


Step 4:
Skin, Re-inforcement & Lifting Hook Application
Once the Skin has been applied all the Divinycell/Klegecell stiffeners are placed on the skin this is done as the resin is curing to give maximum bond.The lifting hooks are glassed in on this stage so they can be used at a later date to release the pool off the mould.These will be glassed over again for maximum strength.


Step 5:
Re-inforcement & Additional Skin
The reinforcement is now implemented, covering the entire surface area of the Divinycell/Klegecell, stiffeners, and hooks. An additional layer of fibreglass is applied to enhance their strength. Subsequently, the material is carefully rolled to eliminate any trapped air within the glass, ensuring a smooth and flawless finish.
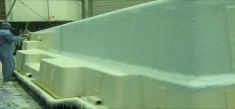

Step 6:
Curing & Release From Mould
The pool is constructed and, once it has fully cured, it will be released from the mold for trimming and detailing. During the pool construction process, brick ties are strategically positioned in the coping. This allows for secure integration of the pool into the concrete bond beam when it is installed in the ground. Here is a 8.5m Venice pool currently being released from the mold, utilising the hooks that were incorporated into the pool structure during its construction.
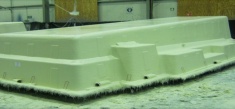
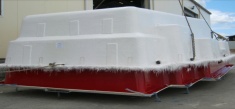
Step 7:
Trimming, Final Inspection & Detailing
A 7.2m Venice pool is positioned on drums for trimming, detailing, and undergoing the final quality control inspection. Prior to leaving the site, the skimmer box is cut and the main drain hole is drilled. As a precautionary measure, we retain the cut-out section of the skimmer box as a sample, along with the pool number, shape, size, and all comprehensive production records. These records are carefully filed for future reference, if needed.
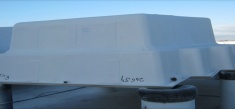
Step 8:
Finished Pool Ready For Delivery
The 7.2m Venice pool is prepared for loading onto the truck, as it is ready for delivery. Prior to departure from the site, the truck driver diligently reviews all paperwork to verify the accuracy of the pool’s details, ensuring everything is in order.
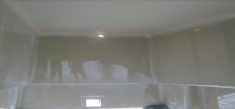